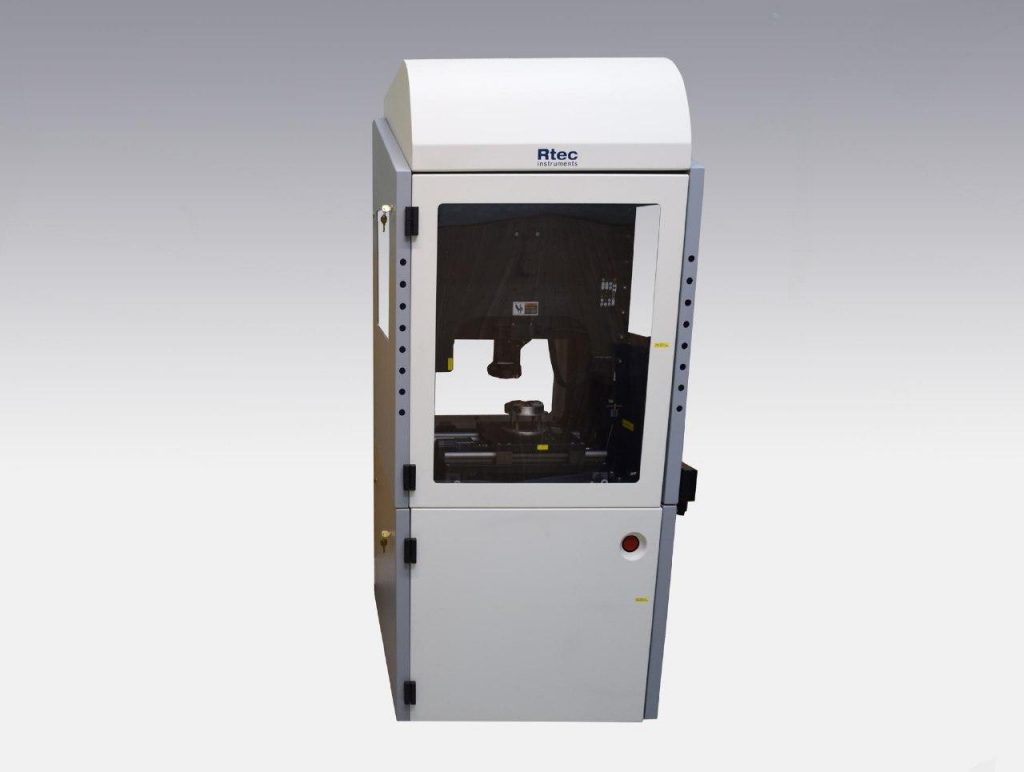
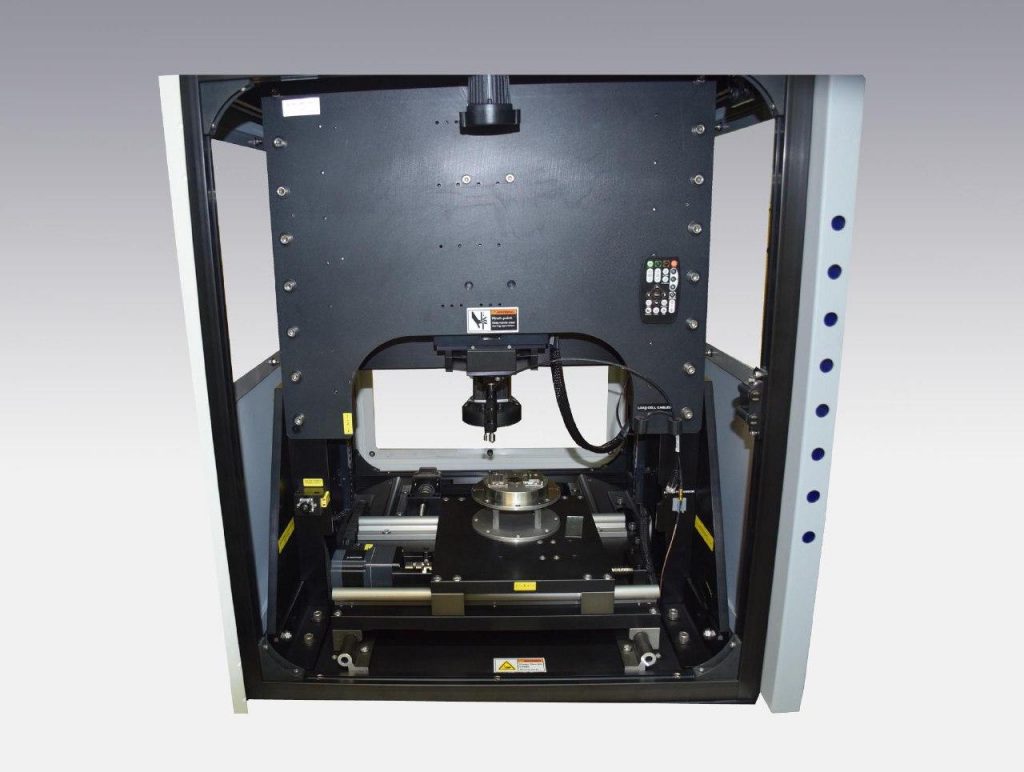
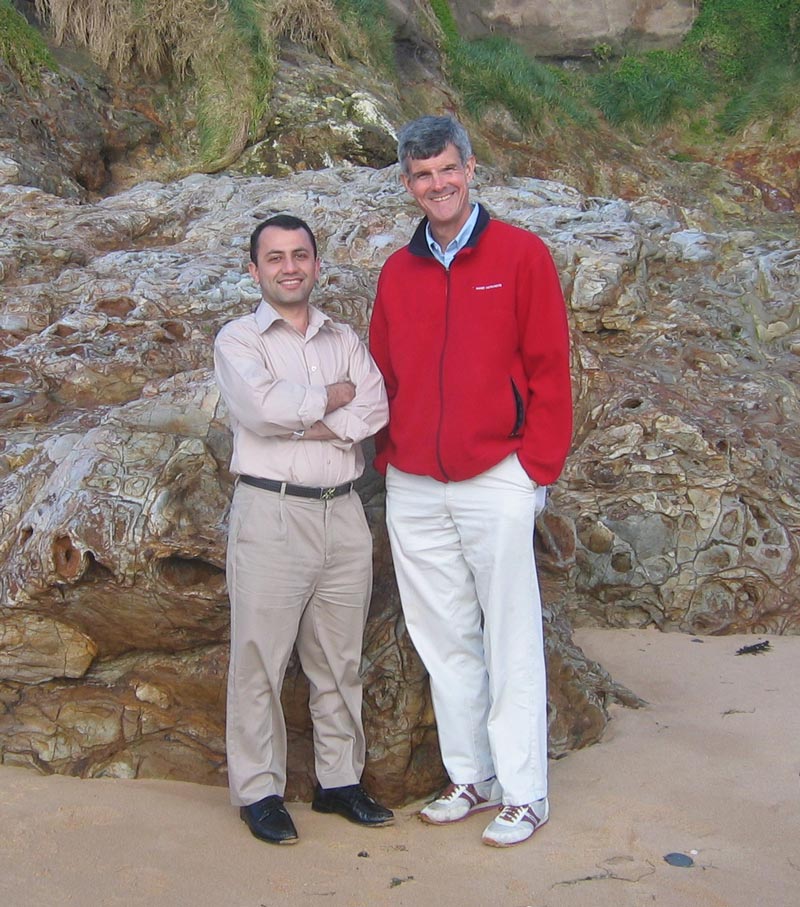
Hardness measurements
The metals handbook defines hardness as the resistance of metals to plastic/permanent deformation. To the metallurgist, it means resistance to penetration. To the lubricant engineer, it indicates resistance to wear. It is also called flow stress by design engineers. Mineralogists interpret hardness as the resistance to scratching. Hardness measurements are one of the most common tests in determining the mechanical properties of materials. This test is easy, quick, inexpensive and repeatable. It is important to recognise that hardness is an empirical test and therefore hardness is not a fundamental property of a material and its values are arbitrary. This is because there are several different hardness tests that will each determine a different hardness value for the same piece of material.
A common question relates to the importance of the test. What is the main purpose of hardness testing? The principal goal of the hardness test is to determine the suitability of a material for a specified application. There is also the relationship between hardness and other properties of materials such as elastic modulus / stiffness, fracture toughness, tensile strength, brittleness, residual stresses and yield strength. It is convenient to do a hardness test and then convert the result to obtain other properties such as tensile strength.
Hardness
The ratio of applied force to contact surface area has been defined as the hardness. Many researchers have modified hardness test; however, the principle has remained the same. Hardness can be measured as macro-, micro- or nano-scale according to the applied forces and obtained displacements. Macro-hardness refers to testing with applied loads of thousands of Newtons. In micro-hardness testing, applied loads are in milli-Newtons. With the help of new technology, the hardness of coatings, thin films and surface layers of materials 100-200 nm deep can be measured. This utilises nanoindentation instrument techniques with very small loads, on the order of nano-Newtons: a nano-hardness test.
Hardness measurements usually fall into three main categories: scratch hardness, rebound or dynamic hardness, and indentation hardness. Details of these methods for measuring the hardness will now be covered.
Scratch file method
In this method one material produces a scratch on the other. In 1822, the Mohs scale of hardness (Mohs 1822) was introduced for minerals which measures relative hardness of ten minerals. The scale of hardness in Mohs test is based on resistance to scratching and cutting of one brittle material by another. On Mohs scale the softest mineral, talc, was given a score of one and diamond, the hardest, was given a score of ten. The hardness is determined from the width or depth of the resulting scratch. In operation, the mineral being tested is scratched by the diamond, and the scratch is compared with standard limit scratches in the microscope eyepiece. The harder material shows the smaller scratch. Unfortunately, the Mohs scale is not linear; that is, each increment of one in the scale doesn’t indicate a proportional increase in hardness. Another type of scratching method is the Cutting method. A sharp tool of a given shape is used to remove a chip of standard dimensions from the surface of the work piece being tested. In abrasion tests, a work piece is loaded against a rotating disk and the rate of wear is the measure of hardness. The hardnesses of grinding wheels are measured with this test. In the Plowing method, a blunt element is moved across the surface of the work piece. Both load and shape are controlled. One can also measure hardness from the width of a groove; the Bierbaum test is an example (Bierbaum 1930). Besides their difficulty of operation, scratching processes are a complicated function of the elastic, plastic and frictional properties of the surface and hence not found in significant practical use.
Rebound method
Dynamic hardness refers to the resistance of a metal to local indentation when the indentation is produced by a rapidly moving indenter. In calculating dynamic hardness, the energy of rebound and change in the volume of the indentation are usually taken into account. A method to determine the hardness of a wide variety of rubber and soft plastics was introduced in 1918, namely the Shore Rebound test (Shore 1918). In this method, a diamond-tipped hammer in a graduated glass tube is allowed to fall from a known height on to the specimen. The hardness number depends on the height to which the hammer rebounds. A harder material has a higher rebound and a greater resistance. This method is also used extensively for hardness measurements on large work pieces or for applications in which visible or sharp impressions in the test surface cannot be tolerated. Twelve scales are used in this method for a wide range of materials, from small rubber O-rings to very soft foam products. Another type of dynamic hardness test is damping. In this method, hardness is determined by the change in amplitude of a pendulum having a hard pivot, which rests on the surface of the work piece being tested. The hardness is measured by the damping produced as the pendulum swings from side to side. The Herbert Pendulum test is an example (Herbert 1923).
There are several standards to define these tests: ASTM D-2240, DIN 53 505, ISO 7619 part 1, JIS K 6301 and ASKER C-SRIS-0101. Non-destructiveness, inexpensiveness, ease of use and applicability to a wide range of materials are their advantages. Some disadvantages are that the test surface must be large enough, and errors in measured values may arise from the indenter not being exactly perpendicular to the test surface.
Indentation method
This technique is the most widely used in determining hardness. Generally, an indenter is pressed into the surface of the work piece to be tested with a specific load and a measurement is made of the size or depth of the indentation. The indenter is made of hard steel, tungsten carbide or diamond shaped into a sphere, cone or pyramid. The Brinell, Meyer, Rockwell, Vickers and Knoop hardness tests are examples. The location of the indent, surface orientation, surface preparation, tip material and the indenter size all play important roles (Johnson, Kendall et al. 1971, Corcoran, Colton et al. 1997, Bahr, Watkins et al. 1998, Hay and Pharr 1998, Kiely and Houston 1998).
Brinell hardness test
Dr. Johan August Brinell, a Swedish engineer, introduced the Brinell hardness test in Sweden in 1900 (Wahlberg 1901). The oldest of the hardness test methods in common use today, the Brinell test is frequently used to determine the hardness of forgings and castings that have an overly coarse grain structure. They are frequently done on large parts and can be used on almost any metallic material. In the Brinell test, hardness is determined by the impression created by forcing a specific indenter (a hard steel or carbide sphere of a specified diameter) into the test material under a specific force for a given length of time. However, in higher automated Brinell testing systems, hardness is evaluated by depth of the impression. By varying the test force and ball size, nearly all metals can be tested using a Brinell test.
The machine applies a load of 500 kg for soft metals such as copper, a 1500 kg load for aluminium castings and a 3000 kg load is used for materials such as iron and steel. Brinell tests are usually defined in ASTM E10 and ISO 6506 standards. The thickness of the specimen should be at least 10 times the depth of the indentation for hard metals and 15 times the depth for softer metals. Also, the specimen should be about 4 times wider than the diameter of the impression. The Brinell number, which varies from 50 BH to 750 BH for metals, can be found as follows:
Where, “P” is imposed load in kgf, “D” is the diameter of the spherical indenter in mm, and “d” is the diameter of the resulting indenter impression in mm. A well-structured Brinell hardness number looks like “50 BH 10/3000/15”, which means that a Brinell hardness of 50 was obtained using a 10 mm diameter hardened steel with a 3000 kg load applied for a period of 15 seconds. The weakness of the Brinell test is the need to measure the indent size optically. Also, indentation requires about 30 seconds. However, a wide range of ball sizes and test forces, which cover most applications and are non-destructive (the sample can normally be reused) are strengths of this method.
Meyer hardness test
In 1908, a quantity to measure the hardness was proposed by Meyer (Meyer 1908). This quantity was the ratio of the load to the projected area of the indentation, which is equal to the mean pressure between the surface of the indenter and the indentation. This quantity is referred to as the Meyer hardness and is expressed in kg/mm2:
In this method, akin to the Brinell hardness test, a hard spherical indenter is pressed into the surface of the specimen under a load of “P” in kgf. It is noted that “d” is the diameter of resultant indentation in mm.
Rockwell hardness test
Stanley P. Rockwell invented the Rockwell hardness test in 1919. It has become the most popular hardness test in use today, mainly because it overcomes the limitations of the previously-mentioned methods.
The Rockwell hardness test is based on the net increase in the depth of the impression as a load is applied. Hardness numbers have no units and are commonly given in the A, B, C, D etc. scales. There are thirty different scales. A higher number in each of the scales means a harder material.
The majority of applications are covered by the Rockwell B and C scales. The Rockwell B test, for soft materials such as copper alloys, soft steel and aluminium alloys, employs a 1/16-inch diameter steel ball with a 10kgf load. In testing harder materials like hard cast iron and hardened steel, a 120-degree sphere-conical diamond indenter is used with up to 140 kgf. An example is ‘80 HRC’, which indicates that the specimen has a hardness reading of 80 on the C scale.
The hardness testing of plastics is most commonly measured by the Rockwell hardness test or Shore hardness test. The Rockwell version is generally chosen for harder plastics such as nylon, polycarbonate and polystyrene.
In this test, a minor load of 10 kgf is first applied into the surface, on top of which is added a major force, which could be 60, 100 or 150 kgf. When the deformation ceases, the major load is removed and the Rockwell hardness number is read directly from a dial gauge. The application of a minor force helps to lessen the effects of poor surface preparation and of any peculiarities in the mechanical properties of the surface skin. With this method, one measures the metals’ resistance to penetration like with the Brinell test; however, the depth of the impression is measured rather than the diametric area. Rockwell testing methods are defined in the following standards: ASTM E18 metals, ISO 6508 metals and ASTM D785 plastics.
Vickers hardness test
The Vickers test was developed in England at Vickers, Ltd., in 1925 and was formerly known as the Diamond Pyramid Hardness test. To cover all testing requirements, there are two force ranges: micro, which is from 10 g to 1000 g and macro, which is from 1 kg to 100 kg. One of the main advantages of this method is that the same indenter shape is used for both ranges; therefore, Vickers hardness values are continuous for metals over the range typically from HV100 to HV1000. The indenter employed in Vickers test is a square-based pyramid with opposite faces at an angle of 136 degrees. This indenter was suggested by Smith and Sandland (Smith and Sandland 1924). The Vickers testing method is similar to the Brinell test. Rather than using the Brinells’ steel ball-type indenter and calculating the hemispherical area of impression, the Vickers machine uses a penetrator that is square in shape, but tipped in one corner so it has the appearance of a playing card “diamond”.
Vickers values are considered force-independent with the exception of forces below 200 g in the absence of micro-cracks (i.e. Ceramics). This means that Vickers values will be the same if tested using a 500 g force or a 50 kg force. The Vickers test is defined in the following standards: ASTM E384 (micro force ranges: 10 g to 1 kg), ASTM E92 (macro force ranges: 1 kg to 100 kg) and ISO 6507-1, 2, 3 (micro and macro ranges). As well as the advantage of utilising the same indenter shapes for all force ranges, the Vickers test is non-destructive. However; the test is very slow and, more significantly, the indent size must be optically measured. This requires that the test point be highly finished to allow a clear image for accurate measurement. Above all, the Vickers machine is a floor-standing unit that is rather more expensive than the Brinell or Rockwell. The Vickers hardness number can be calculated using:
Where, “P” is the force applied to the indenter in kgf and “d*” is the mean diagonal of the indentation in mm.
- Knoop hardness test
The United States National Bureau of standards developed the Knoop hardness test in 1934. This test has been known as a micro-hardness test because forces vary only from 10 g to 1000 g. By using lower indentation loads than the Vickers hardness test, designed for measuring metals, the Knoop test allows the hardness testing of brittle materials such as glass and ceramics. In this test, a microscope is necessary to measure the indent size, requiring a well-polished test surface. Therefore, Knoop is almost always a destructive test. This test method is defined in ASTM E384 and ASTM D-1474 (hardness of organic coatings) standards.
An asset of this test is that test values are mostly force-independent over 100 g; one scale covers all hardness ranges. Another is that low-test forces and the elongated diamond indenter allow testing of very small parts. The Knoop hardness number can be found by the following formula:
where, “P” is the applied load in Kgf and “L” is the measured length of the long diagonal of the indentation in mm. In the most general of terms, for a given material and load, a Vickers indenter may penetrate approximately twice as much and the diagonal dimension may be approximately 1/3 of that achieved by a Knoop indenter (Knoop, Peters et al. 1934).
Spherical indenter
One possible indenter geometry in indentation testing is a sphere. This type of indenter is finding increasing popularity since it provides a smooth transition from elastic to plastic deformation. Spherical indenters enable us to determine the degree of work hardening and provide information about the elastic limit or yield stress and also deduce its stress-strain characteristics. However, obtaining high-quality spheres made from hard, rigid materials at the micron scale is very difficult.
Conical indenter
Another indenter geometry that is rarely used in nanoindentation testing is the cone. The possible reason for this is that it is difficult to manufacture conical diamonds with sharp tips on a small-scale. Thus, they are usually used for modelling rather than experiments. However, this type of indenter is attractive because of the lack of complication associated with the stress concentrations at the sharp edges of the indenter.
Pyramidal indenter
The most frequently used pyramidal indenters in indentation testing are Berkovich, Vickers, Knoop and cube-corner.
The Berkovich indenter is a three-sided pyramid that can be ground to a single point. The face angle of the Berkovich indenter normally used in indentation testing is 65.27o (Berkovich 1951). Another type of pyramidal indenter is the Vickers. The Vickers indenter is a four-sided pyramid with the same depth to area relation as the three-sided Berkovich. The face angle of the Vickers indenter is 68o. Another important indenter geometry is the Knoop. This four-sided pyramidal indenter has two different angles of 172o30’ and 130o respectively. The longer diagonal is about 7 times as large as the shorter diagonal, allowing testing of very hard materials. A longer diagonal line could be more easily measured for shallower depths of residual impression. It is also worth mentioning that the Vickers test is less sensitive than the Knoop test to surface variations, as the Vickers indenter penetrates the surface about twice as far as the Knoop indenter for the same load. Furthermore, the Knoop indenter often produces satisfactory indentations in materials such as glass, which are not easily penetrable by the Vickers pyramid or by a spherical indenter.
The final indenter geometry commonly used is the cube-corner indenter. This indenter is similar to the Berkovich indenter but has a face angle of 35.26o. One can estimate the fracture toughness on a small scale with the help of the cube-corner indenter. This is a result of the high stress and strain this indenter produces in the vicinity of the contact, which is useful in inducing very small cracks around hardness impressions. A summary of the mentioned indenters, shapes and parameters describing their geometries are given in the following Table 1 and Figure 1.
Table 1. Projected area, Face angle and geometry factors for various types of indenters (*Based on King, 1987)
Figure 1. Schematic geometry of 3 and 4 sided indenters with different face angles (courtesy Micro Star Technology)
There has been considerable interest in the last decade in understanding the mechanical characterization of thin film systems. All above-mentioned conventional hardness testers are in the range of macro- and micro-scale. Large errors are introduced due to measurement, when the indentations are too small. The advent of depth-sensing testing/instrumented indentation known as nanoindentation, has enabled the depth of penetration to be measured on the order of nano-metres, while the applied load is usually on the order of micro-Newtons. This makes it possible to obtain reliable values of hardness for thin films. This technique is now discussed in detail since nanoindentation is the main procedure that will be performed in this study.
The study of mechanical properties of thin films has emerged as an important focus in the strength of materials. Perhaps the simplest and the most direct way to probe these properties is by nanoindentation. Since indentation load-displacement data contain a wealth of information, one can simply extract several other mechanical properties such as elastic modulus, stiffness, yield stress, fracture toughness, time dependent deformation effects and residual stresses from a curve of a loading-unloading cycle, Figure 2.
Figure 2. Typical load-displacement curve indicating the final and maximum depth
Nanoindentation is slightly different from current macro-scale hardness tests and requires a number of crucial attentions to obtain accurate data. The value of this method over traditional methods is the simultaneous recording of both elastic and plastic deformations of the sample. The basis of this method is the contact mechanics first theorized by Hertz (Hertz 1881). He demonstrated that the radius of contact “a” is related to the combined radius of the indenter, “R”, the applied load, “P”, and reduced modulus, “Er”, as follows:
Figure 3 shows the cross section of a flat surface and a rigid spherical indenter with the total depth of penetration “h”.
Figure 3. Schematic of the contact between a flat surface and a rigid spherical indenter
The basic assumption is that during the initial withdrawal of the indenter, the contact area between the indenter and the specimen remains constant. In 1965, another major contribution was made by Sneddon (Sneddon 1965). He introduced general relationships among the load, displacement and contact area for any punch, Figure 4.
Figure 4. A schematic representation of a section through an indentation showing various quantities used in the analysis (Oliver & Pharr, 1992)
He derived a simple expression to determine the contact stiffness as the increment of load and displacement:
Contact stiffness can also be written as a function of reduced modulus and projected contact area (Sneddon 1965). Thus, contact stiffness, which is also called the Sneddon Stiffness equation, becomes:
The correction factor: A constant that takes into account the geometry of the indenter is included as follows:
This equation was derived for an axisymmetric indenter, with circular contact. The correction factor β plays a very important role. In 1987, different values for β were found for different geometries by King (King 1987). For indenters with circular contacts like spherical and conical indenters, β=1. For indenters with square cross sections like the Vickers and Knoop, β=1.012, and for triangular cross sections like Berkovich and cube-corner indenters, β=1.034. Oliver and Pharr followed Sneddon’s analysis for the indentation of linear-elastic by rigid punches (Oliver and Pharr 1992). It is presumed that the initial unloading is an elastic event during which the contact area remains constant. Recent studies have shown that yet another small correction factor may be needed in very precise work. Vlassak and Nix (Vlassak and Nix 1994) conducted independent numerical calculations for the flat-ended triangular punch and found a higher value than previously cited, β=1.058. A year after that, Hendrix (Hendrix 1995) used simple elastic analysis procedures and found β=1.0055 for Vickers and β=1.0226 for Berkovich. In 1996, Larsson et al. (Larsson, Ginnakopoulos et al. 1996) conducted full 3D finite element calculations for a purely elastic material and introduced a formula to find the correction factor in terms of Poisson’s ratio. Finite element simulations and experimental studies have also been used to evaluate β and explore what factors influence it (Gao and Wu 1993, Bolshakov and Pharr 1997, Bolshakov and Pharr 1998, Cheng and Cheng 1998, Hay, Bolshakov et al. 1998, Hay and Pharr 1998, Hay, Bolshakov et al. 1999). The wide range of values for β reported in these studies makes it difficult to settle on a single preferred value; however, from these studies, Oliver et al. (Oliver and Pharr 2004) concluded that β for the Berkovich indenter should be slightly greater than unity and for the conical indenter β=1.05
- Hardness
Doerner and Nix were the first to produce the most comprehensive method for determining hardness and modulus from load-displacement curves on the nano-metre scale (Doerner and Nix 1986). Their approach was based on the observation that the initial unloading is linear, which was justified by experimental data from some materials. However, Oliver and Pharr conducted load- and displacement-sensing indentation tests on a large number of materials and found that the initial unloading more closely resembled the behaviour of the power law, and that unloading curves are rarely linear even in the initial stages of unloading (Oliver and Pharr 1992). Thus, the unloading stiffness “S” was calculated by fitting the unloading curve to the power law:
Where, “a” and “m” are power law fitting constants, and “h” and “hf” are depth at maximum load and final depth, respectively, Figure 4. Using the power law relationship for unloading, the hardness of the material can be defined as:
Therefore, hardness can be estimated by computing the mean pressure under the indenter at the point of maximum load, when the projected area is known. In practice, several items affect nanoindentation test data; measuring the contact area is one of them. It can be inferred from the above equation that any error in measuring contact area will lead to error in the hardness value. Thus, the contact area of the indentations must be precisely known to make an accurate measurement of hardness.
Determination of contact area
Doerner and Nix described a calibration method using Transmission Electron Microscopy images of indentations (Doerner and Nix 1986). The areas of indentations were measured by using a graphics tablet and software for calculating the area of closed curves. However, this method is somewhat inconvenient, being both expensive and time-consuming. Another method was introduced by Oliver and Pharr (Oliver and Pharr 1992), which begins by fitting the unloading portion of load-displacement data to the power-law relation. The method is based on the measurement of contact stiffness and requires no imaging of the indentation. It is also based upon an assumption of total compliance (reciprocal of the stiffness) (Pharr, Oliver et al. 1992).
“Cm” and “Cc” are the compliances of the testing machine and of the contact between the indenter and the sample respectively. If the modulus is constant, a plot of Ct vs. A-1/2 is linear for a given material, and the intercept of the slope is a direct measure of the machine compliance. To find the area function and the machine compliance, the authors take advantage of the fact that relatively large indentations can be made in aluminium because of its low hardness. The area function for an ideal Berkovich indenter is given:
By fitting “A” vs. “hc” data, an initial guess at the area function is given:
Where “C1” through “C8” are constants. The first term describes a perfect Berkovich indenter; others describe deviations from the Berkovich geometry due to blunting at the tip. This procedure must be applied several times until convergence is achieved.
- Elastic Modulus
The two mechanical properties measured most frequently by the nanoindentation method are hardness and elastic modulus. Because the unloading curve is dominated by elastic displacement, it is possible to determine the indentation modulus of the material being indented from the slope of unloading curve. The effects of the indenter on the load-displacement curve can also be accounted for by defining the reduced modulus as follows (Johnson 1985):
Where “E” and “ν” are the elastic modulus and Poisson’s ratio respectively of the sample and “Ei” and “νi” are the same definition for the indenter.
As can be inferred from the previous sections, the beauty of the nanoindentation technique lies in measuring the residual deformation indirectly to determine the mechanical properties. Therefore, anything that affects the accuracy of the projected area measurements then makes the hardness and modulus values inaccurate. Some possible sources of errors that can arise during nanoindentation, especially with these measurements of area, are now discussed.
Ultimate tensile strength
There is an established correlation between hardness and tensile strength. When an indenter presses on to the surface of a specimen under examination, the specimen is first deformed elastically. As the load increases, the onset of plastic deformation occurs. At this stage the mean pressure, Pm, reaches a value of 1.1Y (Y is the yield stress). As the load is further increased, the mean pressure increases and material around the region of contact flows plastically. At this stage the mean pressure reaches a value of 3Y; however, it remains constant at this value even if the load is further increased and the indenter sinks further into the specimen (Tabor 1951). The ultimate tensile strength of an ideal plastic metal is essentially the same as the yield stress. Tabor (Tabor 1951) introduced the correlation of Brinell and Vickers hardness and ultimate tensile strength for fully worked-hardened metals:
Brinell Hardness = (2.7-2.8) x Ultimate Tensile Strength
Vickers Hardness = (2.9-3) x Ultimate Tensile Strength
Fracture toughness
Evans and Charles (Evans and Charles 1976), on the basis of dimensional analysis of the underlying fracture-mechanical principles and experimental data, showed that the relation between fracture toughness and ratio of crack to indentation size exhibited universal behaviour. For median cracks (c/a>2.5), the following formula was introduced:
where “KIC” is the Mode “I” critical stress intensity factor, “Φ” is a constant (≈3), “H” is the hardness, “E” is the Young’s modulus, “V” is the half-diagonal of the Vickers indenter and “c” is the radius of the surface crack. As curve-fitted by Blendell (Blendell 1979), this universal behaviour can be expressed:
The application of indentation techniques to the evaluation of fracture toughness was examined by Lawn et al. (Lawn, Evans et al. 1980). They provide an equation for general application:
where “ψ” is a material-independent constant that must be calibrated by indentation of well-characterized materials and “P” is the peak load. Anstis et al. (Anstis, Chantikul et al. 1981) found that a value of ψ=0.016 was appropriate for Vickers diamond pyramid indenter. The empirical constant was also found 0.016 for Berkovich-type indenters (Pharr, Harding et al. 1993). The empirical constant “ψ” for a cube-corner tip is taken as 0.04 by Pharr (Pharr 1998) or 0.032 by Riester (Riester, Bridge et al. 1998).
Brittleness
Another correlation links hardness with brittleness index. Lawn and Marshall (Lawn and Marshall 1979) outlined the following formula:
where, “B”, “H” and “KIC” are brittleness index, hardness and fracture toughness, respectively.
Residual Stress
Residual stress, tensile or compressive, reduces the fatigue strength and fracture properties of bulk metals. These stresses may be generated by any of the following operations: mechanical working (i.e. grinding, rolling, milling, forging, polishing, turning, etching, etc.), ion implantation, case hardening, laser treatment, shot peening, laser shock peening, local plastic deformation, or inhomogeneous heat treatment (Noyan and Cohen 1985). Since 1932, the estimation of residual stresses has been a topic of considerable scientific interest in a wide variety of engineering applications including thin films, thin layers, and surface coatings. However, the origins of residual stresses are not fully understood. In the case of coatings and thin layers and films, the residual stress dominates the mechanical properties (Lu and James 1996, Eberhardt, Pandey et al. 1997, Fang and Lo 2000, Karlsson, Hultman et al. 2000, Uhlmann and Klein 2000), Figure 5. Therefore, measuring the exact value and direction of residual stresses is essential.
Figure 5. The indentation load-depth curves for the surfaces with and without residual stresses (Suresh & Giannakopoulos, 1998)
In 1932, for the first time, the effect of residual stress on hardness measurements was demonstrated by Kokubo, when he studied several materials subjected to applied tensile and compressive uniaxial stress (Kokubo 1932). Since then, a range of methods have been introduced and available for the estimation of residual stresses: Hole Drilling (Rendler and Vigness 1966), Displacement or Substrate Curvature (Doerner, Gardner et al. 1986), Optical Fluorescence (Ma and Clarke 1993), X-ray and Neutron Diffraction (Hehn, Zheng et al. 1995), Ultrasonic, Piezospectroscopy, Beam Bending, Electromagnetic, Positron Annihilation, Nuclear Hyperfine, Chemical Etchant, Fracture Surface Analysis, Strain gage and Layer Removal (Ruud 1982, Marshall and Lawn 1985, LaFontain, Yost et al. 1990, Bergman and Nemanich 1995, Perry, Sue et al. 1996).
However, the above-mentioned techniques have some problems and are somewhat restricted in their applications. Problems include stress relaxation during sampling, their destructive and time-consuming nature, measurement inaccuracies, spatial resolution attainable, possibility of a rough surface, identification of local variations in residual stress, ease of measurement and applicability to a wide range of materials. Also, many of them are expensive, complicated and applicable for only special purposes. Therefore, the development of an alternative and non-destructive method for probing and measuring residual stresses on macro-, micro- and nano-scales is of great interest.Over the last three decades, indentation testing has been used as a conventional method for measuring residual stresses. The effects of residual stress using macro-indentation could be used to locally measure the residual stresses in the surface of metals (Sines and Carlson 1952). Underwood introduced another way to determine the level and nature of residual stresses using surface displacements around an indentation, from the shape of the pile-up occurring at the edge of the contact area (Underwood 1973). Twenty years later, other researchers used Hertzian indentation to estimate the residual surface stress using the following relationship (Chaudhri and Phillips 1990, Chandrasekar and Chaudhri 1993):
Where “P*” and “P” are the loads that produce cracks of the same radius “C” in tempered glass containing a residual stress, and in the annealed glass, respectively. Also, for a Vickers indenter, the indenter geometrical constant is:
There is a threshold for sharp indenters below which cracking will not occur in most brittle materials (Harding, Oliver et al. 1995). For the Vickers indenter, Zeng and Rowcliffe (Zeng and Rowcliffe 1994) reported the cracking thresholds in most ceramic materials to be about 250 mN or more with crack lengths of more than 14 mm. Thus, above equation is unsuitable for investigations involving small volumes of materials, or those encountered in a micro-Vickers regime.
The basic features of the problem were not fully understood until the innovation of nanoindentation techniques and numerical methods. Nanoindentation has been found to be particularly useful for measuring the mechanical properties such as Young’s modulus, yield strength, strain-hardening exponent, tensile strength and hardness, both in general and in the presence of residual stresses. More recently, several studies on how to measure the residual stress by nanoindentation have been undertaken and it has been found that the effect of residual stress on the indentation load-depth curves may help in the measurement of residual stress by depth-sensing indentation (LaFontain, Paszkiet et al. 1991, Bolshakov, Oliver et al. 1996, Tsui, Oliver et al. 1996, Taljat, Zacharia et al. 1998, Karlsson and Larsson 2001, Karlsson and Larsson 2001). Tsui et al. used nanoindentation techniques to investigate the influence of uniaxial and biaxial in-plane stresses on the hardness and elastic modulus measurements (Tsui, Oliver et al. 1996). They found that the hardness and elastic modulus are essentially independent of the residual stress level. This observation was then verified by a finite element simulation (Bolshakov, Oliver et al. 1996).
Suresh and Giannakopoulos (Suresh and Giannakopoulos 1998) outline a simple method for measuring residual stress with sharp, geometrically-similar indenters based on results by (Bolshakov, Oliver et al. 1996, Tsui, Oliver et al. 1996). They proposed a method for the determination of surface residual stresses based on the difference in contact areas and indentation penetration depths of residual-stressed and unstressed samples indented to the same depth. In this method, residual stresses are assumed to be equibiaxial and uniform over a depth (beneath the indented surface) which is at least several times longer than the indentation contact diameter (Suresh and Giannakopoulos 1998). They estimated surface residual stresses in elastoplastic solids on the basis of continuous, quantitative sharp indentation (i.e. Vickers, Berkovich pyramid or circular cone), and the direction of the residual stress-induced normal load. One can obtain residual stress/strain and yield stress by solving simultaneously the following equations:
where, “Y”, “σy” and “σR” are yield stress, yield strength and yield strength of materials with residual strain respectively; “Pmax”, “hmax” and “Amax” are quantities at maximum load; “hf” is unloading depth; “α” is the angle of indenter tip, which is 22o for the Vickers tetragonal pyramid indenter and 24.7o for the Berkovich trigonal pyramid indenter; “C*” is 1.220 for Vickers and 1.273 for Berkovich.
However, effects of residual stress on the contact areas are relatively small for a sharp indenter. It is not clear that the method can be practically applied since no experimental verification has been provided. In contrast, Taljat and Pharr (Taljat and Pharr 2000) have recently suggested that much larger effects from residual stress can be measured using nanoindentation with blunt, spherical indenters. At the onset of plastic deformation, the mean pressure, reaches a value of 1.1Y. Thus :
Pm = 1.1 (Y-σR ). One can easily extract the residual stress as follows:
Where “Y” is the yield stress; “Er” is the reduced or indentation modulus; and “R” and “a” are radius of a spherical indenter and the contact radius, respectively. They have also reported the results of a finite element study showing that indentation load-displacement behaviour in the transition regime between elastic contact at small loads and fully developed plastic contact at large loads is affected by residual stress in a potentially measurable way.
In a further development of the previous method, Swadener et al. (Swadener, Taljat et al. 2001) proposed contact pressure, instead of contact area, as a stress indicator using a spherical indenter. The two new experimental techniques are based on spherical indentation, which in certain deformation regimes can be much more sensitive to residual stress than indentation with sharp pyramidal indenters.
The first method requires that the yield stress be known and also the contact pressure at the onset of yielding, determined experimentally. Based on theory developed by Hertz (Hertz 1896), mean contact pressure, “Pm”, is equal to P/πa2 =(4Era)/(3πR), reflecting the deformation behaviour up to the load at which yielding first occurs. However, after yielding has initiated, the Tabor (Tabor 1951) relation can be used to relate the mean pressure to the effective flow stress, “σf”.
Here, “Pm” is the mean contact pressure, and “ψ” is the constraint factor, which is 1.07 at the onset of yielding (Johnson 1970). Tabor (Tabor 1951) suggested that when the plastic strains in the vicinity of the contact are large compared to the elastic strains, the constraint factor reaches a plateau value of 2.8. Previous equation can be re-written as follows:
where, “a” is the contact radius; “σy” is the yield strength; “R” is the radius of a rigid spherical indenter; “σR” is the residual stress; and “Er” is the effective elastic modulus.
The second method is based on the contact pressure and requires a specimen in a known stress state. In this method, mean contact pressure is Pmax/πa2. Residual stress can be estimated from the following empirical equation, which is related to the mean contact pressure and the constraint factor for stressed specimens:
The second method has the advantage of not requiring the yield strength in advance. If the variation of “ψσf” can be established by experiments, then residual stress can be determined from measurements of the indentation contact pressure. However, Lepienski et al. (Lepienski, Pharr et al. 2004) believe that these two methods are not easily applied to thin film/layer structures, while a recent study has shown that the substrate effect is negligible when the coating is softer than the substrate and the indentation depth is less than half of the coating thickness (Chen and Vlassak 2001). Lee and Kwon (Lee and Kwon 2002) analyzed the residual stresses of a thin film/coating with the help of nanoindentation techniques. With their proposed equation, the residual stress can be evaluated from the changes in contact shape and applied load during stress relaxation under the condition of constant indentation depth. Thus, one can evaluate the residual stress in a thin film by dividing the residual-stress-induced normal load, “Lres”, by the contact area:
where residual stress-induced normal load, “Lres”, is the differential load: “Lo-Lt” for tension and “Lo-Lc” for compression (“Lo”, “Lc” and “Lt” are the applied load at the stress-free state, compressive stress, and tensile stress states respectively). They found that the values from this technique agreed well with the values from the conventional curvature method. It is noted that the average value of the surface residual stress can be measured using the conventional curvature method with the following equation:
Where “E”, “t” and “ν” are the elastic modulus, thickness, and Poisson’s ratio of the substrate, respectively; and “tf” and “R” are the film thickness and curvature radius.
Most recently, a depth-sensing indentation method to measure the residual stress using sharp indenters was used (Wang, K.Ozaki et al. 2006). The energy contribution of the residual stresses could be approximately calculated from the residual indentation impression for an equibiaxial residual stress state:
where “α” is the cone semi-angle of the residual indentation impression; and “P1” is the maximum load of the residual stressed sample while “P2” is the coincide loading portion of stress-free sample with unloading portion of stressed sample, Figure 6. In their theoretical analysis, they assumed that elastic unloading responses during indentation are fully independent of any pre-existing residual stress at the indented surface. One needs to conduct a FEA to estimate the geometric correction factor “α”, which is found 65.3o for Berkovich indenter.
Figure 6. The loading and unloading curves of the stressed sample and loading curve of stress free sample (Wang et al., 2006)
As can be inferred from the mentioned studies, most of the methods introduced requiring a yield strength that does not exist in brittle materials. Others are either at a theory or FEA stage, encountered in micro-regimes. Therefore, indentation techniques need to be extended from the micro-regime to the nano-regime for measuring residual stresses of brittle materials. Pharr found that a cube-corner indenter could fulfil that need (Pharr 1998), by using the cube-corner indenter cracking threshold for most brittle materials of about 1 mN (Harding, Oliver et al. 1995, Pharr 1998). Based on Anstis’ model (Anstis, Chantikul et al. 1981) for measuring fracture toughness and equation 25, and also by taking into account the influence of residual stresses, a new model was introduced for measuring the unknown residual stresses using a cube-corner indenter (Zeng and Rowcliffe 1994, Zeng, Ginnakopoulus et al. 1998):
Here, “co” and “c” are lengths of the radial crack of a stress-free sample and a sample with residual stresses, respectively; and “φ” is a crack geometry factor which is 1.77 (Lawn 1993). A tensile residual stress will act to extend the stress-free crack, so that
c > co, while a compressive residual stress will shorten it, so that c < co, (Kese and Rowcliffe 2003).
- Pile-up and sink-in
When plastic deformation occurs, two phenomena associated with nanoindentation, pile-up (hc>h) and sink-in (hc<h), have been found to have significant effects on the measurements of the indentation modulus and hardness, Figure 7. For non-strain-hardening materials with a large value of Elastic modulus/Yield stress, the plastic zone is observed to have a hemispherical shape meeting the surface well outside the radius of the circle of contact. Pile-up in these materials is to be expected (Fischer-Cripps 2002). When pile-up occurs, the contact area is greater than that predicted and the usual Oliver and Pharr method of determining the hardness cannot be accurate enough, since use of such a method would underestimate the contact area and overestimate the hardness, sometimes by as much as 50-100% (Tsui, Ross et al. 1997, Bolshakov and Pharr 1998). For materials with a low value of E/Y, like glasses and ceramics, the plastic zone is typically contained within the boundary of the circle of contact. This makes the projected contact area smaller than the cross-sectional area of the indenter at that depth. Sinking-in is more likely to occur in these materials (Fischer-Cripps 2002). In this case, contact area is overestimated and hardness is underestimated by Oliver & Pharr’s method. On the other hand, Bolshakov and Pharr (Bolshakov and Pharr 1998) utilized the ratio of the final depth (hf) over the maximum depth (hmax). For entirely elastic materials the ratio is equal to zero, while for a purely plastic response the ratio would be unity. They also found that all materials with a ratio below 0.7 experience sink-in, regardless of their ability to work-harden, while materials with a ratio over 0.7 experience pile-up. The amount of pile-up corresponds to the size of the plastic zone or the load applied. Above all, by eliminating the contact area from previous Equations, we get:
Joslin and Oliver (Joslin and Oliver 1990) were the first to use the P/S2 parameter in their study of mechanical properties of ion-implanted Ti alloys. For homogenous materials, H and E are usually constant with indentation depth. As a result, P/S2 is also constant with indentation depth. Thus, this parameter is a direct measure of the true hardness, since it is proportional to H. Page et al. have also used this term to characterize coated systems (Page, Pharr et al. 1998). Analysing P/S2 provides a more complete picture of the nanoindentation properties of a film/substrate system than can be obtained using the Oliver-Pharr method alone. Another independent relation has also been introduced based upon work hardening. Cheng and Cheng (Cheng and Cheng 1998, Cheng and Cheng 1998, Cheng and Cheng 1999) used finite element simulations of a wide variety of elastic-plastic materials with different work-hardening behaviours, since the amount of pile-up and sink-in depends on the work-hardening characteristics of the material.
Figure 7. Effects of piling-up and sinking-in on the actual contact area for penetration of the same depth. A) Cross-sectional view; B) Plan view
- Rouphness
Real surfaces are not ideally flat. On macro- and micro- scales, roughness has little effect on indentation testing (Tabor 1951); however, surface roughness does play an important role in testing on the nano-scale. Roughness can lead to significant error in determining the area of contact between the indenter and the substrate. Figure 8 illustrates how a rough surface can create several points of contact with an indenter. The effect is to increase the displacement and decrease the hardness value compared to a smooth surface. In order to overcome the obstacle that roughness presents, several researchers have addressed the nature of friction between surfaces (Archard 1957, Greenwood and Williamson 1966, Greenwood and Tripp 1971). Furthermore, Bobji and Biswas used finite element analysis to investigate the role of surface roughness on nanoindentation experiments (Bobji, Biswas et al. 1997, Bobji and Biswas 1998). They found that roughness remarkably increases the scatter in hardness, especially at small depths.
Figure 8. Schematic of a contact between an indentation tip and a rough surface
Johnson developed a roughness parameter, which quantifies the surface roughness (Johnson 1985). From the suggested equation, not mentioned here, it may be concluded that for light loads with spherical indenters, surface roughness may play a significant role. However, for a sharp indenter (say a tip radius of 100 nm), the effect of roughness is less important. The recommended way to measure the hardness, which is less sensitive to the effect of surface roughness, is with the Joslin and Oliver model that is based upon the ratio of P/S2.
- Indentation size effect
Results from several recent indentation studies reveal that hardness increases remarkably for small indentations (sub-micrometer depth regime), while on a larger length scale (>100 nm), values are found to decrease with increased depth of indentation. This is called the indentation size effect (ISE) (Fleck, Muller et al. 1994, Ma and Clarke 1995, Qing and Clarke 1995, McElhaney, Vlassak et al. 1998, Liu and Ngan 2001, Tymiak, Kramer et al. 2001). Thus, the value of hardness, and also modulus, may be experimentally observed to be different when different indentation depths occur. The most commonly used method to investigate this effect is the Nix and Gao model (Nix and Gao 1998). Their model for conical indenters in terms of the Taylor law is based upon on geometrically necessary dislocations created within the plastic zone. Their following model describes the depth dependence of hardness of crystalline materials, which is following the derivations of Stelmashenko et al. (Stelmashenko, Walls et al. 1993) and De Guzman et al. (DeGuzman, Neubauer et al. 1993):
Here, “H0” is the hardness when the indentation depth becomes indefinitely large (macroscopic hardness) and “h0” is a length scale for depth-dependence of hardness as follows:
The ISE characteristic length “ho” in the Nix-Gao (Nix and Gao 1998) model is:
where “δ” is a constant to be taken as 0.5, “µ” is the shear modulus, “b” is the Burgers vector, and “ρs” is the density of statistically-stored dislocations. It should be pointed out that these equations have successfully modelled micro indentation and have been undergoing development (Gao, Huang et al. 1999, Huang, Gao et al. 2000).
Recently, Swadener et al. (Swadener, George et al. 2002) found that the model gives a good prediction for large indentations, but overestimates hardness for small indentation depths. Their experimental results support that hardness increases with decreasing depth of penetration; however, for a spherical indenter, they showed that hardness is not affected by depth, but increases with decreasing sphere radius. They extended the Nix and Gao model to indenters of various shapes as follows:
For conical indenters: h0 =3ṝ tan2 θ/2bρs
For spherical indenters: h0 =ṝ/bρs
“ṝ” is the Nye factor. Peierls stress was found to be important for materials with a significant friction stress by Qiu et al. (Qiu, Huang et al. 2001). Thus, the previous equation could be modified to:
where “HP” is a constant equal to 3√3ΤP where, “ΤP” is the Peierls stress. Above all, a comprehensive study has been done on the indentation size effect in single crystals, polycrystals and amorphous solids using the Vickers micro-hardness test (Manika and Maniks 2006).
- Indenter deformation & tip rounding
Other possible sources of error in nanoindentation testing may include deformation of the indenter and/or tip rounding. A sharp three-sided Berkovich diamond pyramidal indenter has a tip radius of approximately 100nm, but tip rounding can occur after repeated use, Figure 9. These two possible phenomena have been given considerable attention in the recent published literatures (McElhaney, Vlassak et al. 1998, Gong, Miao et al. 2004, Jager 2004, Warren and Guo 2006). Gong et al. (Gong, Miao et al. 2004) found that the deviations of the determined area from the perfect Berkovich indenter may be due to the indenter tip rounding and the deformation of the indenter. Their experimental values demonstrate that the hardness determined using the Oliver and Pharr model is an overestimated value due to the neglect of the indenter deformation. Recent FEA results show that more force is required to achieve the specified indentation depth with increased tip radius (from 0, perfectly sharp, to 150nm) (Warren and Guo 2006). Therefore, tip rounding becomes important in indentation testing on thin films of less than about 500 nm thickness and when the maximum depth of penetration is in the order of 50 nm (Fischer-Cripps 2002). Figure 9A illustrates the indenter tip is now shorter than the ideal one (Figure 9B) by the tip defect Dh. The depth hi at which the spherical tip meets the flat face of the cone is given by:
Where “α” is the half-included angle of the indenter (70.32o for Berkovich).
Figure 9. Schematic representation of a nanoindentation, A) Rounded indenter, B) Ideal indenter
Creep
Another phenomenon requiring attention is creep. Elastic-plastic behaviour is usually assumed in nanoindentation testing. However, some materials have viscoelastic properties that can influence the load-displacement value. Time-dependent plasticity, or creep, is often observed in indentation testing as continued deformation during the hold at maximum load. Changes in the unloading slope caused by material creep may influence the calculated modulus since the modulus is correlated to the unloading slope of the load-displacement curve.
Anstis, G. R., P. Chantikul, B. R. Lawn and D. B. Mashall (1981). “A critical evaluation of indentation techniques for measuring fracture toughness: I, direct crack measurements.” Journal of the American Ceramics Society 64(9): 533-538.
Archard, J. F. (1957). “Elastic deformations and the law of friction.” Proceedings of Royal Society London A243: 190-205.
Bahr, D. F., C. M. Watkins, D. E. Kramer and W. W. Gerberich (1998). “Yield point phenomena during indentation. In fundamentals of nanoindentation and nanotribology.” Materials Research Society Symposium 522: 83-88.
Bergman, L. and R. J. Nemanich (1995). “Raman and photoluminescence analysis of stress state and impurity distribution in diamond thin films.” Applied Physics 78: 6709-6719.
Berkovich, E. S. (1951). “Three-faced diamond pyramid for micro-hardness testing.” Industrial Diamond Review 11(127): 129-133.
Bierbaum, C. H. (1930). “Hardness determined by microcut.” Metal Progress 18: 42-44.
Blendell, J. E. (1979). PhD dissertation PhD, Massachusetts Institute of Technology.
Bobji, M. S. and S. K. Biswas (1998). “Estimation of hardness by nanoindentation of rough surfaces.” Materials Research 13(11): 3227-3233.
Bobji, M. S., S. K. Biswas and J. B. Pethica (1997). “Effect of roughness on the measurement of nanohardness-a computer simulation study.” Applied Physics Letters 71(8): 1059-1061.
Bolshakov, A., W. C. Oliver and G. M. Pharr (1996). “Influences of stress on the measurement of mechanical properties using nanoindentation: Part II: finite element simulations.” Materials Research 11(3): 760-768.
Bolshakov, A. and G. M. Pharr (1997). “Inaccuracies in Sneddon’s solution for elastic indentation by a rigid cone and their implication for nanoindentation data analysis. In thin films-stresses and mechanical properties.” Materials Research 436: 189-194.
Bolshakov, A. and G. M. Pharr (1998). “Influences of pileup on the measurement of mechanical properties by load and depth sensing indentation techniques.” Materials Research 4: 1049-1058.
Chandrasekar, S. and M. M. Chaudhri (1993). “Indentation cracking in soda-lime glass and Ni-Zn ferrite under Knoop and conical indenters and residual stress measurements.” Philosophical Magazine A 67(6): 1187-1218.
Chaudhri, M. M. and M. A. Phillips (1990). “Quasi-static cracking of thermally tempered soda-lime glass with spherical and Vickers indenters.” Philosophical Magazine A 62(1): 1-27.
Chen, X. and J. J. Vlassak (2001). “Numerical study on the measurement of thin film mechanical properties by means of nanoindentation.” Materials Research 16: 2974-2982.
Cheng, Y. T. and C. M. Cheng (1998). “Relationships between hardness, elastic modulus, and the work of indentation.” Applied Physics Letters 73: 614-616.
Cheng, Y. T. and C. M. Cheng (1998). “Scaling approach to conical indentation in elastic-plastic solids with work hardening.” Applied Physics 84: 1284-1291.
Cheng, Y. T. and C. M. Cheng (1999). “Scaling relationships in conical indentation of elastic-perfectly plastic solids.” Solids and Structure 36: 1231-1243.
Corcoran, S. G., R. J. Colton, E. T. Lilleodden and W. W. Gerberich (1997). “Anomalous plastic deformation at surface: nanoindentation of gold single crystals.” Physical Review B 55(24): 16057-16060.
DeGuzman, M. S., G. Neubauer, P. Flinn and W. D. Nix (1993). “The role of indentation depth on the measured hardness of materials.” Materials Research Symposium Proceedings 308: 613-618.
Doerner, M. F., D. S. Gardner and W. D. Nix (1986). “Plastic properties of thin films on substrates as measured by submicron indentation hardness and substrate curvature techniques.” Materials Research 1: 845-852.
Doerner, M. F. and W. D. Nix (1986). “A method for interpreting the data from depth-sensing indentation instruments.” Materials Research 1: 601-609.
Eberhardt, A. W., R. Pandey, J. M. Williams, J. J. Weimer, D. Ila and R. L. Zimmerman (1997). “The roles of residual stress and surface topography on hardness of Ti implanted Ti-6Al-4V.” Materials Science and Engineering A 229: 147-155.
Evans, A. G. and E. A. Charles (1976). “Fracture toughness determinations by indentation.” American Ceramics Society 59: 371-372.
Fang, W. and C.-Y. Lo (2000). “On the thermal expansion coefficients of thin films.” Sensors and Actuators A 84: 310-314.
Fischer-Cripps, A. C. (2002). Nanoindentation. New York, Springer-Verlag.
Fleck, N. A., G. M. Muller, M. F. Ashby and J. W. Hutchinson (1994). “Strain gradient plasticity: theory and experiment.” Acta Materialia 42: 475-487.
Gao, H., Y. Huang and W. D. Nix (1999). “Modeling plasticity at micrometer scale.” Naturwissenschaften 86: 507-515.
Gao, H. J. and T. W. Wu (1993). “A note on the elastic contact stiffness of a layered medium.” Materials Research 8: 3229-3232.
Gong, J., H. Miao and Z. Peng (2004). “On the contact area for nanoindentation tests with Berkovich indenter.” Materials letters 58: 1349-1353.
Greenwood, J. A. and J. H. Tripp (1971). “The contact of two nominally rough surfaces.” Proceedings of the Institution of Mechanical Engineers 185: 625-633.
Greenwood, J. A. and J. B. P. Williamson (1966). “Contact of nominally flat surfaces.” Proceedings of Royal Society London A295(1442): 300-319.
Harding, D. S., W. C. Oliver and G. M. Pharr (1995). Cracking during nanoindentation and its use in the measurement of fracture toughness. Materials Research Society Symposium Proceedings, Warrendale, PA, Materials Research Society.
Hay, J. C., A. Bolshakov and G. M. Pharr (1998). “Applicability of Sneddon relationships to the real case of a rigid cone penetration an infinite half space. In fundamentals of nanoindentation and nanotribology.” Materials Research 522: 263-268.
Hay, J. C., A. Bolshakov and G. M. Pharr (1999). “Critical examination of the fundamental relations used in the analysis of nanoindentation data.” Materials Research 14: 2296-2305.
Hay, J. C. and G. M. Pharr (1998). “Experimental investigations of Sneddon’s solution and an improved solution for the analysis of nanoindentation data. In fundamentals of nanoindentation and nanotribology.” Materials Research Society 522: 39-44.
Hehn, L., C. Zheng, J. J. Mecholsky and C. R. Hubbard (1995). “Measurement of residual stresses in Al2O3/Ni laminated composites using an X-ray diffraction technique.” Materials Science and Engineering A 30: 1277-1282.
Hendrix, B. C. (1995). “Use of shape correction factors for elastic indentation measurements.” Materials Research 10: 255-257.
Herbert, E. G. (1923). Engineer 135: 686.
Hertz, H. (1881). “On the contact of elastic solids.” Reine and Angewandte Mathematik 92: 156-171.
Hertz, H. (1896). Miscellaneous papers. London, Macmillan.
Huang, Y., H. Gao, W. D. Nix and J. W. Hutchinson (2000). “Mechanism based strain gradient plasticity II. Analysis.” Mechanics and Physics of Solids 48: 99-128.
Jager, I. L. (2004). “Surface free energy-a possible source of error in nanohardness.” Surface Science 565: 173-179.
Johnson, K. L. (1970). “The correlation of indentation experiments.” Mechanics and Physics of Solids, 18: 115-126.
Johnson, K. L. (1985). Contact mechanics. Cambridge, U.K., Cambridge University Press.
Johnson, K. L., K. Kendall and A. D. Roberts (1971). Surface energy and the contact of elastic solids. Proceedings of the Royal Society, London.
Joslin, D. L. and W. C. Oliver (1990). “A new method for analyzing data from continuous depth-sensing microindentation tests.” Materials Research 5: 123-126.
Karlsson, L., L. Hultman and J. E. Sundgren (2000). “Influence of residual stresses on the mechanical properties of TiCxN1-x (x=0, 0.15, 0.45) thin films deposited by arc evaporation.” Thin Solid Films 371: 167-177.
Karlsson, S. and P. L. Larsson (2001). “On the determination of the residual stress and strain fields by sharp indentation testing. Part I: Theoretical and numerical analysis.” Acta Materialia 49: 2179-2191.
Karlsson, S. and P. L. Larsson (2001). “On the determination of the residual stress and strain fields by sharp indentation testing. Part II: Experimental investigation.” Acta Materialia 49: 2193-2203.
Kese, K. and D. Rowcliffe (2003). “Nanoindentation method for measuring residual stress in brittle materials.” Journal of the American Ceramic Society 86(5): 811-816.
Kiely, J. D. and J. E. Houston (1998). “Nanomechanical properties of Au (111), (001) and (110) surfaces.” Physical Review B 57(19): 12588-12594.
King, R. B. (1987). “Elastic analysis of some punch problems for a layered medium.” Solids Structure 23: 1657-1664.
Knoop, F., C. G. Peters and W. B. Emerson (1934). A sensitive pyramidal-diamond tool for indentation measurements. Research Paper RP1220, U.S. Dept. Commerce: 211-240.
Kokubo, S. (1932). “Change in hardness of plate caused by bending.” Science reports of the Tohoku Imperial University 21(2): 256-267.
LaFontain, W. R., C. A. Paszkiet, M. A. Korhonen and C. Y. Li (1991). “Residual stress measurements of thin aluminium metallization by continuous indentation and x-ray stress measurement techniques.” Materials Research 6: 2084-2090.
LaFontain, W. R., B. Yost and C.-Y. Li (1990). “Indentation load relaxation experiments with indentation depth in the submicron depth.” Materials Research 5: 776-781.
Larsson, P. L., A. E. Ginnakopoulos, E. Soderlund, D. J. Rowcliffe and R. Vestergaard (1996). “Analysis of Berkovich indentation.” Solids Structure 33: 221-248.
Lawn, B. R. (1993). Fracture of brittle solids. Cambridge, U.K., Cambridge University Press.
Lawn, B. R., A. G. Evans and D. B. Marshall (1980). “Elastic/Plastic indentation damage in ceramics: The median/Radial crack system.” American Ceramic Society 63(9-10): 574-581.
Lawn, B. R. and D. B. Marshall (1979). “Hardness, toughness and brittleness: an indentation approach.” American Ceramics Society 62: 347-350.
Lee, Y. H. and D. Kwon (2002). “Residual stresses in DLC/Si and Au/Si systems: Application of a stress-relaxation model to the nanoindentation technique.” Materials Research 17(4): 901-906.
Lepienski, C. M., G. M. Pharr, Y. J. Park, T. R. Watkins, A. Misra and X. Zhang (2004). “Factors limiting the measurement of residual stresses in thin films by nanoindentation.” Thin Solid Films 447-8: 251-257.
Liu, Y. and A. H. W. Ngan (2001). “Depth dependence of hardness in copper single crystals measured by nanoindentation.” Scripta Materialia 44(2): 237-241.
Lu, J. and M. R. James (1996). Hand book of Measurement of Residual Stresses. Lilburn, GA, Fairmount Press.
Ma, Q. and D. R. Clarke (1993). “Optical fluorescence from chromium ions in sapphire: A probe of the image stress.” Acta Metallurgica et Materialia 41: 1811-1816.
Ma, Q. and D. R. Clarke (1995). “Size dependent hardness in silver single crystals.” Materials Research 10: 853-863.
Manika, I. and J. Maniks (2006). “Size effects in micro- and nanoscale indentation.” Acta Materialia 54(8): 2049-2056.
Marshall, D. B. and B. R. Lawn (1985). “Indentation of brittle materials.” ASTM Special Technical Publication 889: 26-46.
McElhaney, K. W., J. J. Vlassak and W. D. Nix (1998). “Determination of indenter tip geometry and indentation contact area for depth-sensing indentation experiments.” Materials Research 13(5): 1300.
McElhaney, K. W., J. J. Vlassak and W. D. Nix (1998). “Determination of indenter tip geometry and indentation contact area for depth-sensing indentation experiments.” Journal of Materials Research 13(5): 1300.
Meyer, E. (1908). “Zeits. d. Vereines Deutsch.” ingenieure 52: 645.
Mohs, F. (1822). Grundriss der mineralogic. Dresden.
Nix, W. D. and H. J. Gao (1998). “Indentation size effects in crystalline materials: a law for strain gradient plasticity.” Journal of the Mechanics and Physics of Solids 46(3): 411-425.
Nix, W. D. and H. J. Gao (1998). “Indentation size effects in crystalline materials: a law for strain gradient plasticity.” Mechanics and Physics of Solids 46(3): 411-425.
Noyan, I. C. and J. B. Cohen (1985). Residual Stress: Measurement by diffraction and interpretation. New York, Springer-Verlag.
Oliver, W. C. and G. M. Pharr (1992). “An improved technique for determining hardness and elastic modulus using load and displacement sensing indentation experiments.” Materials Research 7: 1564-1583.
Oliver, W. C. and G. M. Pharr (2004). “Measurement of hardness and elastic modulus by instrumented indentation: advances in understanding and refinements to methodology.” Materials Research 19: 3-20.
Page, T. F., G. M. Pharr, J. C. Hay, W. C. Oliver, B. N. Lucas, E. Herbert and L.Riester (1998). “Nanoindentation characterization of coated systems: P/S2-a new approach using the continuous stiffness technique.” Materials Research Society Symposium 522: 53-64.
Perry, A. J., J. A. Sue and P. J. Martin (1996). “Practical measurement of the residual stress in coatings.” Surface and Coatings Technology 81: 17-28.
Pharr, G. M. (1998). “Measurement of mechanical properties by ultra-low load indentation.” Materials Science Engineering A 253: 151-159.
Pharr, G. M., D. S. Harding and W. C. Oliver (1993). Measurement of fracture toughness in thin films and small volumes using nanoindentation methods. Mechanical properties and deformation behavior of materials having ultra-fine microstructures, Dordrecht, Netherlands, Kluwer Academic Press.
Pharr, G. M., W. C. Oliver and F. R. Brotzen (1992). “On the generality of the relationship between contact stiffness, contact area, and elastic modulus during indentation.” Materials research 7: 613.
Qing, M. and D. R. Clarke (1995). “Size dependent hardness of silver single crystals.” Materials Research 10(4): 853-863.
Qiu, X., Y. Huang, W. D. Nix, K. C. Hwang and H. J. Gao (2001). “Effect of intrinsic lattice resistance in strain gradient plasticity.” Acta Materialia 49(19): 3949-3958.
Rendler, N. J. and I. Vigness (1966). “Hole-drilling strain-gage method of measuring residual stresses.” Experimental Mechanics 6: 577-586.
Riester, L., R. J. Bridge and K. Breder (1998). “Fracture toughness of SiC determined using nanoindentation. In fundamentals of nanoindentation and nanotribology. In fundamentals of nanoindentation and nanotribology.” Materials Research Society Symposium 522: 45-50.
Ruud, C. O. (1982). “Nondestructive and semi destructive methods for residual stress measurement.” ASTM Special Technical Publication 776: 3-5.
Shore, A. F. (1918). “Report on hardness testing: Relation between ball hardness and scleroscope hardness.” Iron and Steel Institute 2: 59-75.
Sines, G. and R. Carlson (1952). “Hardness measurements for determination of residual stresses.” ASTM Bulletin 180: 35.
Smith, R. L. and G. E. Sandland (1924). An accurate method of determining the hardness of metals with particular reference to those of high degree of hardness. Proceedings of the Institution of Mechanical Engineers.
Sneddon, I. N. (1965). “The relation between load and penetration in the axisymmetric boussinesq problem for a punch of arbitrary profile.” International Journal of Engineering Science 3: 47-56.
Sneddon, I. N. (1965). “The relation between load and penetration in the axisymmetric boussinesq problem for a punch of arbitrary profile.” Engineering Science 3: 47-56.
Stelmashenko, N. A., M. G. Walls, L. M. Brown and Y. V. Milman (1993). “Microindentations on W and Mo oriented single crystals: An STM study.” Acta Materialia 41(10): 2855-2865.
Suresh, S. and A. E. Giannakopoulos (1998). “A new method for estimating residual stresses by instrumented sharp indentation.” Acta Materialia 46: 5755-5767.
Swadener, J. G., E. P. George and G. M. Pharr (2002). “The correlation of the indentation size effect measured with indenters of various shapes.” Mechanics and Physics of Solids 50(4): 681-694.
Swadener, J. G., B. Taljat and G. M. Pharr (2001). “Measurement of residual stress by load and depth sensing indentation with spherical indenters.” Materials Research 16(7): 2091-2102.
Tabor, D. (1951). The hardness of metals. Oxford, United Kingdom, Clarendon Press.
Taljat, B. and G. M. Pharr (2000). “Measurement of residual stresses by load and depth sensing spherical indentation.” Materials Research Society Symposium 594: 519-524.
Taljat, B., T. Zacharia and G. M. Pharr (1998). “Pile-Up behaviour of spherical indentations in engineering materials.” Materials Research Society Symposium 522: 33-38.
Tsui, T. Y., W. C. Oliver and G. M. Pharr (1996). “Influences of stress on the measurement of mechanical properties using nanoindentation: Part I: Experimental studies in an aluminium alloy.” Materials Research 11(3): 752-759.
Tsui, T. Y., C. A. Ross and G. M. Pharr (1997). “Nanoindentation hardness of soft films on hard substrates: effects of the substrate.” Materials Research Society Symposium 473: 57-62.
Tymiak, N. I., D. E. Kramer, D. F. Brhr, T. J. Wyrobek and W. W. Gerberich (2001). “Plastic strain and strain gradients at very small indentation depths.” Acta Materialia 49(6): 1021-1034.
Uhlmann, E. and K. Klein (2000). “Stress design in hard coatings.” Surface and Coatings Technology 131: 448-451.
Underwood, J. H. (1973). “Residual stress measurement using surface displacements around an indentation.” Experimental Mechanics 30: 373-380.
Vlassak, J. J. and W. D. Nix (1994). “Measuring the elastic properties of anisotropic materials by means of indentation experiments.” Mechanics and Physics of Solids 42: 1223-1245.
Wahlberg, A. (1901). “Brinell’s method of determining hardness.” International Iron and Steel Institute 59: 243-298.
Wang, Q., K.Ozaki, H. Ishikawa, S. Nakano and H. Ogiso (2006). “Indentation method to measure the residual stress induced by ion implantation.” Nuclear Instruments and Methods in Physics Research B 242: 88-92.
Warren, A. W. and Y. B. Guo (2006). “Machined surface properties determined by nanoindentation: experimental and FEA studies on the effects of surface integrity and tip geometry.” Surface and Coatings Technology 201(1-2): 423-433.
Zeng, K., A. E. Ginnakopoulus, D. Rowcliffe and P. Meir (1998). “Residual stress fields at the surface of sharp pyramid indentations.” Journal of the American Ceramic Society 81(3): 689-694.
Zeng, K. and D. Rowcliffe (1994). “Experimental measurement of residual stress field around a sharp indentation in glass.” Journal of the American Ceramic Society 77(2): 524-530.